天然鳞片石墨的球化原理是天然鳞片石墨颗粒在球化机中发生碰撞、剪切和摩擦等机械作用,大片状颗粒发生塑性变形而成球形和类球形颗粒,而微细颗粒吸附密着在主核上,经摩擦和去棱角化后制得球形石墨。球化处理能够显著地提升天然鳞片石墨的电化学性能。球化的天然鳞片石墨材料具有较小的比表面积,更高的振实密度,从而具有更高的首次库仑效率,更高的可逆比容量及更优异的循环稳定性。天然石墨球化的整个加工过程中由于研磨和碰撞等机械作用会产生许多球化微粉,目前球化工艺工业中产生的球化微粉废料占比为总量的50%~60%,这一部分废料是经过十几次甚至几十次处理后残留下来的,球化微粉因存在振实密度低、比表面积过大、表面缺陷多等问题,所以这部分球化微粉只能用于生产低附加值的润滑剂与耐火材料等,极大降低了天然鳞片石墨的高值化利用,直接影响了球形石墨负极的生产成本。基于此,本工作通过对球化微粉进行纯化、等静压压制、热处理、破碎、筛分等处理,获得了电化学性能优异的石墨负极材料。重点研究了热处理过程的升温速率及保温温度对材料物理性能及各项电化学性能的影响,分析了所得材料的理化及嵌脱锂性能。论文研究工作对于实现天然石墨负极材料生产过程中产生的大量球化微粉的高值化利用具有一定的指导意义。
1 实验材料及制备
1.1 材料制备
(1)球化微粉的纯化:首先配制氢氟酸浓度为3 mol/L、盐酸浓度为3 mol/L的混酸溶液;再按液固比4 mL/g(混酸体积mL/球化微粉g)将球化微粉分散于混酸溶液中,在25 ℃条件下搅拌反应3 h后,通过抽滤操作进行固液分离、去离子水洗涤,将所得滤饼置于80 ℃充分烘干即得球化微粉的纯化样品。
(2)球化微粉的改性:取纯化后的球化微粉与X%的沥青(X=2、5、10、15)称量并置于混料机中混合12 h得到混合样品,然后将混合样品置于液压模具中施加20 kN的压力使其压制成型。将所得的压形材料置于氩气气氛炉中密封后,以150 mL/min的流速持续通入氩气,排气0.5 h后,以5 ℃/min的升温速率加热至250 ℃并保温1 h,再以一定的升温速率Y ℃/min(Y=2、5、10)加热至保温温度Z ℃(Z=600、800、1000)并保温2 h后自然降温至室温。热处理后的样品经常规打散、筛分即得球化微粉的改性样品H-SG/C。根据包覆沥青质量的不同将样品命名为H-SG/C-X,X为不同沥青的添加量;根据升温速率及保温温度的不同将样品命名为SG/C-VY-Z,Y为升温速率,Z为保温温度。
1.2 材料表征
(1)物理性能测试:使用场发射扫描电子显微镜(FESEM,仪器型号为JSM-7900F)观察粉末的形貌;用X射线衍射(XRD,仪器型号为Rigaku-TTRIII,扫描范围为10°~80°,扫描速度为10°/min)分析样品的物相;采用氮气吸附法(仪器型号为Micromeritics ASAP 2020)测定样品的比表面积(BET);采用激光粒度仪(仪器型号为Malvern Mastersizer 2000)分析样品粒度;使用X射线荧光光谱仪(XRF,仪器型号为XRF-1800)分析样品的元素组成。
(2)电化学性能测试:将活性物质、黏结剂(LA-133、CMC)、导电炭黑以92∶3∶3∶2的质量比混合均匀,再加入适量溶剂(无水乙醇和去离子水的混合液),在玛瑙研钵中研磨成均匀浆料,并涂覆于铜箔上,置于120 ℃真空干燥4 h,再将烘干的电极片冲制成直径为10 mm的圆形电极片。以制得的石墨电极为工作电极,金属锂片为对电极,Celgard 2400多孔隔膜为隔膜,采用1 mol/L LiPF6/EC+DMC+DEC溶液为电解液,在充满氩气的手套箱内装配成CR2025扣式电池。在武汉蓝电电池综合测试系统中进行电化学测试,测试电压范围为0.01~2 V。
2 结果与讨论
2.1 球化微粉原料的基本理化性能表征
根据石墨化学分析国家标准GB/T 3521—2008测定了球化微粉的水分、挥发分、灰分以及固定碳含量,如表1所示。
表1 球化微粉原料成分分析
分析表1中的数据可知,球化微粉中杂质含量较多,固定碳含量为91.77%,与当前国标所要求的99.9%以上的固定碳含量要求有较大差距,需要对其进行纯化处理。此外,为了确定杂质的主要成分,对灰分进行XRF测定,结果如表2所示。
表2 球化微粉原料灰分成分及含量
由表2可知,球化微粉中的主要杂质元素为Fe、Si、Ca、S、K、Al、Zn、Cu,这与天然石墨矿中伴生有许多其他矿石有关,如石英(SiO2)、铁矿石(Fe2O3)、高岭石、云母石、铝硅酸钙(CaO·Al2O3·4SiO2·5H2O)等,为了进一步确定球化石墨微粉中杂质存在的化合物形式,对球化微粉原料及其灰分进行XRD测试,所得结果如图1所示。
图1 (a) 球化微粉原料XRD图谱;(b) 球化微粉灰分XRD图谱
从图1(a)原料的XRD衍射图谱可以看出,除了明显的石墨(002)衍射峰外,图谱中还存在许多峰强较低的杂质衍射峰,主要为SiO2、Fe、Zn的衍射峰,说明杂质中可能存在少量单质铁及单质锌元素,由于XRD衍射精度有限,部分杂质含量较低且为无定形状态,无法检测出其成分。但从灰分XRD衍射图谱图1(b)可以知道,杂质中的硅元素主要以石英相SiO2形式存在,铁元素主要以Fe2O3形式存在,部分与钾元素以K2FeO4形式存在,铝元素和钙元素主要以氧化物Al2O3、CaO形式存在,其他杂质多以金属氧化物形式存在,如Fe2O3、Al2O3、CaO、K2FeO4等。故纯化过程主要除去Fe、Si、Ca、Al等杂质元素。
表3为球化石墨微粉原料的振实密度、比表面积和粒度数据。从表中数据可以看出,原料的振实密度较低,仅有0.435 g/cm3,这与球形石墨的生产制备过程相关,低振实密度会导致电池的体积能量密度降低,降低了其续航能力。原料比表面积为11.47 m2/g,过大的比表面积会导致电池的首次库仑效率降低,增加锂损失。原料粒径D50为5.019 μm,相对于常规商业石墨10~15 μm的粒径,此材料的粒径偏小,过小的粒径容易导致电池循环过程中材料粉化,使循环性能快速衰减,但粒径小的石墨中锂离子迁移通道增多,有利于倍率性能的提升。
表3 球化微粉原料振实密度、比表面积、粒度
综合以上分析可知,如能通过适当工艺解决球化微粉振实密度低、比表面积大、粒径小等问题,可以实现其高值化利用。
2.2 混酸纯化对球化微粉的性能影响
图2所示为球化微粉纯化前后的FESEM图,测试结果显示在经过纯化后样品表面形貌基本没有变化,石墨颗粒的尺寸为5~10 μm,片状结构较为明显,表明在前期球形化过程中,小尺寸鳞片石墨并未有效成球。
图2 球化微粉纯化前后的FESEM图
(a) 纯化前;(b) 纯化后
表4为混酸纯化后所得纯化球化微粉的XRF数据,通过对比表2可知,经纯化处理后Fe、Si、Ca等主要杂质的占灰比例明显减少,说明混酸纯化处理达到了良好的除杂效果。
表4 纯化球化微粉灰分成分及含量
表5为混酸纯化后所得材料的灰分、振实密度、比表面积、粒度测试结果,对比表1与表3可知,经纯化处理后材料的灰分降到0.29%,这与表4所得结论一致,而纯化处理过程对材料的振实密度、比表面积、粒度基本无影响。
表5 混酸纯化后所得球化微粉的灰分、振实密度、比表面积及粒度
图3所示为球化微粉纯化前后在0.1 C倍率下的首次充放电曲线。从图3可知,纯化前,球化微粉原料的首次可逆比容量为306.8 mAh/g,首次库仑效率为83.59%;经纯化处理后,所得样品的首次可逆比容量为340.3 mAh/g,首次库仑效率为86.10%。因此,纯化处理过程可以在一定程度上提升材料的首次可逆比容量及首次库仑效率,但提升效果有限,还需要进行后续改性处理。
图3 混酸纯化前后在电流密度为37.2 mA/g下首次充放电曲线
(a) 纯化前;(b) 纯化后
2.3 机械压形及表面包覆的造粒工艺对球化微粉电化学性能的影响
2.3.1 沥青包覆量对材料理化及电化学性能的影响
分析上述混酸纯化处理结果可知,混酸纯化处理可以有效降低石墨微粉中的杂质含量,但纯化后物料依然存在粒度小、比表面积大、振实密度低等缺陷;此外,电化学性能测试表明纯化物料的首次库仑效率仅为86.10%,难以直接应用于锂离子电池。为解决上述问题,需要对球化微粉进行造粒与表面改性处理。考虑到其振实密度低的缺陷,本研究采用机械压形处理,即将纯化后的球化微粉与沥青按一定比例混合均匀,在液压机中进行压制成形,再对所得高压实块体进行热处理,后经破碎、筛分,获得最终的二次颗粒,以综合提升其振实密度、颗粒粒径,同时解决表面结构缺陷、颗粒各向异性等问题。
图4所示分别为沥青包覆量为2%、5%、10%、15%条件下所得样品H-SG/C的FESEM图。当沥青包覆量为2%时,相较于未包覆的球化微粉,形貌基本无差异;当沥青包覆量为5%时,材料形貌更为规整,表面也更光滑,基本为细小颗粒,表明在沥青的造粒作用下,小颗粒实现了较为明显的融合;当沥青包覆量为10%时,颗粒均一度较5%更为明显,表明在此条件下,大部分小颗粒微粉均以粒径较大的颗粒为核心形成更大的颗粒,且表面更为规整光滑;当沥青包覆量为15%时,可以看到所得二次颗粒由较多小颗粒融合而成,这是由于沥青在软化过程中,由于含量过高导致沥青不均匀融化并与一次颗粒发生黏结,少部分区域形成过大颗粒。
图4 不同沥青包覆量的H-SG/C FESEM图
(a) H-SG/C-2;(b) H-SG/C-5;(c) H-SG/C-10;(d) H-SG/C-15
从图5(a)的XRD图谱中可以看出,包覆4种比例沥青的H-SG/C均表现出石墨明显的(002)晶面特征峰,说明沥青碳包覆并没有改变石墨的晶体结构,但从特征峰的强度可以看出,碳包覆会导致特征峰强度降低,且随着沥青包覆量的增大,特征峰强度有不断减弱的趋势,这主要是由于沥青热解形成的无定形碳成分随着沥青用量的增大而升高,这种无定形碳复合在原来的天然石墨结构中,导致复合材料结晶程度被削弱。从图5(b)的XRD放大图中可以看出,沥青碳包覆会导致特征峰左移,这主要是由于沥青热解碳的无定形结构会导致复合材料整体层间距升高,且随着沥青含量的增多,无定形碳包覆量增多,该特征峰左偏移程度变大。
图5 H-SG/C材料的 (a) XRD图谱及其 (b) 26°~27° XRD放大图
表6所列为H-SG/C材料的振实密度、比表面积、粒度的测试结果。从表中可以看到,相较于球化微粉及其纯化样,采用沥青碳包覆可以显著提升振实密度、降低比表面积、提高颗粒粒径,且振实密度随着沥青包覆量的增加而增加,比表面积随着沥青包覆量的增加而减小,颗粒D50尺寸随着沥青包覆量的增加而增大。以上结果表明采用沥青进行液压成形、碳化包覆可以有效解决球化微粉原料存在的振实密度低、比表面积大、颗粒细小的问题。
表6 H-SG/C材料的振实密度、比表面积、粒度
图6为H-SG/C复合材料在0.1 C倍率下的首次充放电曲线,表7所示为其首圈电化学性能相关数据。由图6和表7可知,对比纯化后的球化微粉,沥青碳改性后所得材料的首次库仑效率及首次可逆比容量均有所提升,并且随着沥青包覆量的增加,所得材料的首次可逆比容量增加,首次库仑效率增加,如当沥青包覆量为15%时,H-SG/C-15的首次可逆比容量为355.3 mAh/g,首次库仑效率为91.64%。因此,通过添加沥青进行液压成形、热解碳化造粒,可以降低材料的比表面积、提升材料的振实密度及粒径,从而使得材料表现出高的首次库仑效率及高的可逆比容量。
图6 H-SG/C复合材料在0.1 C倍率下的首次充放电曲线
(a) H-SG/C-2;(b) H-SG/C-5;(c) H-SG/C-10;(d) H-SG/C-15
表7 H-SG/C复合材料0.1 C倍率下的电化学性能
图7为H-SG/C复合材料的循环性能图及其倍率性能图。从图7(a)可以看到,H-SG/C材料在前50圈保持较为稳定的循环性能,比容量均能保持在300 mAh/g左右;当沥青包覆量较少(2%与5%)时,其在循环50圈后呈现快速衰减趋势,当循环至200圈时容量保持率不到30%;H-SG/C-10表现出最为稳定的循环稳定性,循环200圈时的容量保持率在85%以上;而当沥青包覆量为15%时,所得H-SG/C-15在循环100圈后容量开始下降,200圈后的容量保持率为70%,低于H-SG/C-10。从图7(b)倍率性能图中可以看到,H-SG/C材料在0.2 C、0.5 C倍率下性能稳定,可逆比容量均能保持在300 mAh/g以上,但在0.5 C倍率下H-SG/C-10、H-SG/C-15的比容量比H-SG/C-2、H-SG/C-5高出10%左右;在1 C倍率下,H-SG/C-10、H-SG/C-15的比容量可以达到300 mAh/g以上,而H-SG/C-2、H-SG/C-5的比容量不稳定,在2 C、4 C倍率下同样有类似结论;当倍率恢复至0.2 C时电池比容量均能达到350 mAh/g,这说明H-SG/C材料倍率性能优异。
图7 H-SG/C复合材料在不同倍率下的电化学性能图
(a) 0.1 C倍率下的循环性能;(b) 倍率性能
以上分析表明,沥青包覆改性可以提升材料的比容量及循环稳定性,当沥青含量过低时,其改善效果一般,循环50次后容量明显下降;而当沥青包覆量过高时,由于沥青在热融化过程中的不均匀包覆,使得材料包覆效果不好,所得材料的循环稳定性不佳;沥青包覆量为10%时效果最好,所得H-SG/C-10材料表现出较好的循环稳定性及倍率性能。
2.3.2 热处理制度对材料理化及电化学性能的影响
根据上述实验结果可知,材料最优首次库仑效率仅有91.64%,仍有提升空间。考虑到碳化过程的升温速率及保温温度对碳层结构的影响较大,故针对H-SG/C-10材料热处理过程设计如表8所示碳化温度制度,以研究沥青碳化温度及其升温速率对材料造粒包覆效果的影响,以便得到最佳的热处理制度。
表8 不同样品的碳化温度制度
图8是对部分制备材料进行FESEM测试。从图8(a)、(b)可以看出,在升温速率为2 ℃/min时,沥青将小颗粒与大颗粒微粉黏结,且粒径较为均匀,约为10 μm,且600 ℃与1000 ℃下材料形貌类似,但1000 ℃下的材料形貌更为规整,表明温度的升高对材料的形貌影响较小。对比图8(c)与(d)可知,当升温速率增加时,材料会出现部分大颗粒,且在升温速率为10 ℃/min时形状会变得更为不规则,粒径更大,表明过高的升温速率会导致沥青在碳化过程中团聚黏结,来不及均匀流动,产生更大的颗粒,无定形碳在石墨表面的包覆变得不均匀。
图8 不同温度制度下材料的FESEM图
(a) SG/C-V2-600;(b) SG/C-V2-1000;(c) SG/C-V10-600;(d) SG/C-V5-600
表9为不同温度制度下材料的振实密度、比表面积和粒度D50的测试结果。从表中可以看出,随着升温速率的增加振实密度会降低,比表面积和粒度会增大,过快的升温速率会导致沥青快速融化,包覆不均匀,产生较多大颗粒结块,在破碎研磨过程中无定形碳层被破坏,且碳化速率过快会导致沥青中的小分子快速逸出,导致材料产生孔隙,降低振实密度、增大比表面积。相对的慢速碳化过程反应较为平稳,沥青融化速度慢,在石墨微粉表面的包覆效果较好,振实密度提高至0.9 g/cm3以上,比表面积降低至3.15 m2/g,说明包覆效果良好,粒径D50在11.5 μm左右。
表9 不同温度制度下材料的振实密度、比表面积、粒度
图
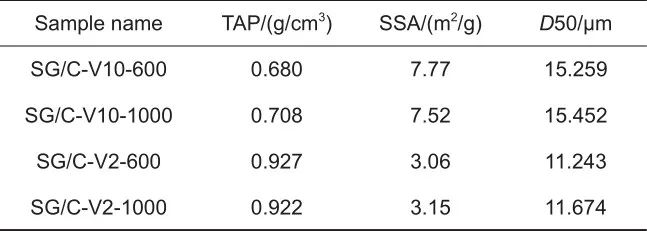
对不同温度制度下制备而得的材料进行扣式半电池性能测试。图9为不同温度制度下材料的首圈充放电曲线。从图中可以看出同一保温温度下,升温速率越慢,首次库仑效率越高,SG/C-V2-1000的首次库仑效率最高,为93.12%,并且比容量依然可以达到350 mAh/g以上,表明升温速率的降低及保温温度的提高可以有效改善材料的造粒包覆效果,进而提高材料的首次库仑效率。
图9 不同热处理制度下复合材料的首次充放电曲线
(a) SG/C-V2-600;(b) SG/C-V2-800;(c) SG/C-V2-1000;(d) SG/C-V5-600;(e) SG/C-V5-800;(f) SG/C-V5-1000;(g) SG/C-V10-600;(g) SG/C-V10-800;(f) SG/C-V10-1000
图10为SG/C-V2-1000在不同测试条件下的电化学性能。从图10(a)的0.2 C倍率下长循环图可知材料的循环稳定性好,在循环400圈后容量保持率为79%。对比图10(b)、(c)和图7(a)、(b),经过慢速造粒的SG/C-V2-1000对比H-SG/C-10,在0.5 C倍率下的循环稳定性有所提升,在200圈循环后有85%的容量保持率,其在0.5 C、1 C倍率下的倍率性能较为优异,且2 C、4 C倍率下循环比容量均有所提升。从图10可知材料的循环稳定性均得到提升,这是由于在慢速碳化条件下,沥青对球化石墨微粉的包覆效果良好,材料结构稳定,在循环过程中不易粉化。
图10 SG/C-V2-1000不同测试条件下的电化学性能
(a) 0.2 C下的循环性能;(b) 0.5 C下的循环性能;(c) 倍率性能
3 结论
(1)球化微粉原料的灰分为5.16%,其片状结构较为明显,石墨颗粒尺寸为5~10 μm;
(2)采用混酸处理法对球化微粉进行纯化处理,纯化过程对材料的表面形貌、振实密度、比表面积和粒度大小并无太大影响;纯化后材料的灰分降为0.29%;在0.1 C倍率下,首次可逆比容量为340.3 mAh/g,首次库仑效率为86.1%;
(3)将纯化后球化微粉与不同比例的沥青混料、压制成形、热处理获得二次颗粒,研究表明经上述改性处理可提高材料的振实密度及颗粒粒径,降低比表面积;电化学测试表明,随着沥青包覆量的增加其首次可逆比容量增加,首次库仑效率增加,当沥青添加量为10%时,表现出最优的电化学性能,其在0.1 C倍率下首次可逆比容量为350.9 mAh/g,首次库仑效率为91.36%,在0.5 C倍率下充放电比容量达到310 mAh/g,循环200圈后容量保持率仍在80%以上;
(4)通过进一步优化热处理制度,可进一步提高球化微粉的电化学性能,以2 ℃/min的升温速率加热至250 ℃保温1 h,再以相同的升温速率加热至1000 ℃并保温2 h后所得的SG/C-V2-1000材料,在0.1 C倍率下首次可逆比容量为352.4 mAh/g,首次库仑效率为93.12%,在0.2 C倍率下循环400圈后的容量保持率为79%,在0.5 C倍率下循环200圈后容量保持率为85%;
(5)本工作通过常规的纯化、压制、热处理、破碎、筛分等流程对球化微粉进行处理,获得电化学性能优异的天然石墨负极材料,对当前天然石墨生产过程中大量产生的球化微粉的高值化利用提供一定的理论基础与借鉴。 碳索储能网 https://cn.solarbe.com/news/20231007/80862.html
责任编辑:caoyang